穴加工における加工コスト削減のポイント
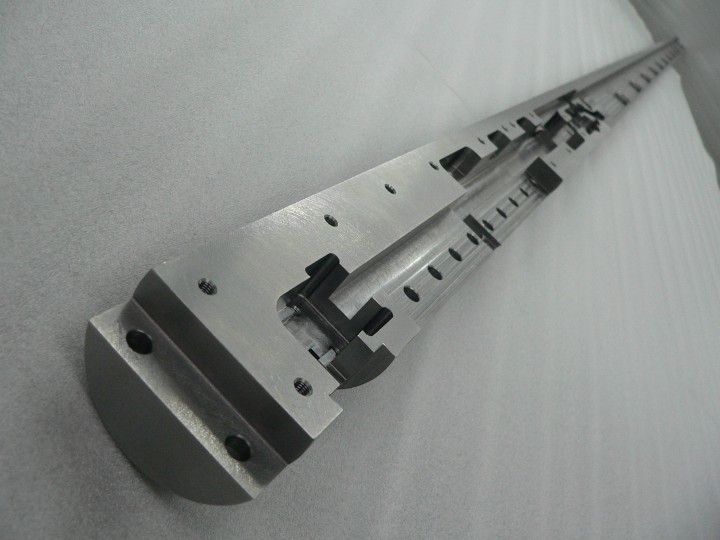
弊社では独自のノウハウ・技術を用いて、
お客様のご要望がどこにあるのかを形状に応じて考慮したうえで、
最適な設計提案を行っております。
最適な設計にて、加工を行う事で、
安定した加工に繋がり、
加工工数の削減やコストダウンを実現します。
今回は、穴加工における加工コスト削減のポイントを一部ご紹介します。
穴加工における逃げ確保のポイント
例えば、厚みが15mmの薄板などに5H7の長穴加工を行う場合、
Φ5以下の小径エンドミルで加工をする必要があります。
この場合、3倍以上の加工を行うため、刃物が逃げてテーパーに仕上がる可能性があります。
しかし、穴形状を段つきにし、逃がしを確保する事で、
切削工具を根元でつかめるため、
倒れを抑える事が可能となります。
その結果、テーパーの発生を防止することができる為、精度出しの工数を削減できます。
長穴加工における精度出しのポイント
例えば、幅10センチ深さ100センチの長穴加工をする場合には長い刃物が必要になります。
長穴加工の先端を加工する場合、
刃物をしっかりと掴むことができないため加工精度を出すことが困難になります。
必要とする先端の加工精度を出すためには、入口の幅を50センチ程度に拡張し、
ツーリングが入るスペースを確保することで、
刃物をしっかりと掴むことが可能となり、少ない工程で高精度の加工を実現できます。
長穴加工における設計のポイント
長穴加工の公式はL/D≦5になります。
L/Dの寸法が5に近づけば近づくほど、加工が難しくなります。
そのため、深い穴加工は切削油のスムーズな送りが出来ず、
刃物が熱を持ちやすく、加工することが困難な場合があります。
そのため、穴の貫通が必要ない場合であれば、
設計段階で貫通穴を両面からの浅い穴加工に変更することで加工工数を削減し、
コストダウンにつなげることが可能になります。
穴加工における精度確保と工数削減のポイント
厚みが20mmのプレートの表と裏に穴あけ加工を必要とする場合、
穴加工を両面に実施すると、
ワンチャックで加工を行うことができずにコストアップにつながります。
そのため、機能的に問題がないのであれば、
穴加工を貫通させることで、複数個ある穴加工を同時に行なうことができ、
加工工数を大幅に削減すると同時に、位置精度も向上させることが可能となります。
長尺ワークにおける高精度穴加工のポイント
60×60×500の長尺ワークへΦ20H7の加工精度にて深穴加工を行う場合、
加工中にチップが欠ける危険性や出口付近では刃物のへたりにより
回転を上げることが出来ず、非常に加工工数が増えてしまいます。
そのため、あらかじめ設計図面上に有効深さを明確に指示することで、
必要な機能を満たすための最適な加工を選択することができます。
逃げをつくる、または、段落としをすることで、
Φ20H7の加工精度は入口の部分だけ必要となるため、
少ない工数にて加工精度を満たすことができます。
その結果、コストダウンにつながります。
最後に
長尺部品加工センターを運営する城陽富士工業では、
ミクロン単位の超高精度加工や横型加工など、お客様のあらゆるニーズにお応えする加工技術を保有しております。
長尺加工に関するお悩みは、是非、当社までご相談ください。
また、城陽富士工業では、
リモート会議システムを活用した「無料オンライン技術相談」も随時行っております。
無料オンライン技術相談をご希望の方は、下記よりお申込みください。